Clearly I did just that, but does it play well? And how’s it sound? Read on while I take you through all the details of how I 3D printed this colorful and very ’80s looking plastic Strat that — spoiler alert — plays and sounds just like a Strat!
Why Print a Guitar?
A lot of people buy 3D printers and end up printing nothing but useless trinkets only to discover that 3D printing is not quite the Star Trek replicator solution that they thought it was. While I’ve certainly printed some useless stuff, I had bigger things in mind.
Then SARS-CoV-2 happened.
A Quick Aside
The Goal
I decided early on that the guitar would be an existing design because while I love technology, I’m not a 3D architect by any stretch, and the software I know how to use is limited to Cura (the slicer) and TinkerCad, a simple free online Computer Aided Design (CAD) tool.
I decided that if I wanted the guitar to be useful, then a Fender-type design was best because if there’s one thing Leo Fender did well, it was make killer guitars that could be bolted together from parts. Along those lines I also decided that I would be using a wooden neck and not 3D-printing that part of the guitar. The neck is the kind of the soul of the guitar, and buying one off the shelf just seemed like the way to go.
Anything metal would be purchased or used from my spare parts bin. Anything plastic, I would print. My goal was to keep this inexpensive, which is honestly something I’m not very good at, an observation that I once again confirmed by the end of the project.
The Printer
No, this is not your run of the mill home printer, but the only thing this printer is really giving me for this project is build volume which translates to the ability to printer larger parts. I didn’t even end up using the dual extrusion capability for this project, though I use it all the time for others.
The Filament
I’m not going to bore you with my reasons for not using Acrylonitrile Butadiene Styrene (ABS), but I did use something called Tough PLA.
If I were to do this again I would entertain other polymers such at PETG but MatterHackers didn’t have it in yellow when I was looking. Honestly, though, after completing the project I am pretty happy with the results in regular old PLA.
The Guitar Model
The Fender Stratocaster and Telecaster are both guitars designed by Leo Fender to be easy to manufacture and repair, and although they couldn’t have dreamt of 3D printing back in the ’50s, the concepts put into place by Leo have stood the test of time. Not only that, but the body shapes are in the public domain these days, much to the consternation of Fender. Since Telecasters and I don’t get along, I decided that the Stratocaster (Strat) shape would be my choice.
Using a Strat body makes the entire process much simpler than if I had chosen, say, a Les Paul because with the Strat Design, very little is actually screwed into the body. The vast majority of parts are attached to the pick guard on a Strat, and the pick guard is then attached to the body. Additionally, my 3D printed guitar could use an actual wooden neck which similarly bolts to the body of the guitar. A Strat was designed to be many pieces screwed together, and by limiting the parts that I needed to 3D print, I could make a guitar that might actually play and sound like a Strat. Plus, I have a lot of guitar parts laying around and as a result I would likely not need to buy any parts. I was wrong about that as you’ll see, but the idea seemed solid at the start of the project.
I’ve posted my final model files on Thingiverse so you can print your own. Remember, the parts are sized for an Ultimaker S5, so check to see if they’ll fit on your printer.
Phase I – The Test Prints
- The pick guard screw holes were way too wide, and not deep enough. Also, maybe three of them were in the right spots.
- The neck screws holes didn’t go all the way through so I had to extend them.
- The bottom of the body under the neck pocket was beveled so much that the neck plate stuck out about 2-3mm on all sides.
- There were no screw holes for the tremolo claw
- There were no screw holes for the strap pegs
- The control cavity didn’t fit the controls
The majority of the changes I made to the model were in the control cavity, so having smaller pieces meant burning less filament every time I printed a new test of the bottom horn piece. That bottom horn piece proved to be a huge pain in my ass.
In the end almost everything worked great except for the bridge screws and the pick guard screw holes. The bridge itself worked OK, but the screws seemed to be cheap pot-metal crap, which I guess I should have expected when paying $20 for a Ping Strat bridge, but one of the screws broke on me and many of the rest stripped, so I pulled them all and ordered hardened Callaham screws from Specialty Guitars, all of which worked great. You’ll see how that broken screw affected me later on.
My goal at the beginning was to use whatever leftover parts I had, but the simple truth is that I’m not really a Strat guy so I don’t have many Strat parts laying around. Somehow I did have pick guard screws, a neck plate, and an output jack plate, likely a result of me gutting the only Stat I’ve ever owned, a 2008 American Deluxe that came with some absolutely awful Samarium Cobalt Noiseless pickups and the S1 switching system along with an ugly green/white pick guard that I just hated.
Phase II – The Final Prints
Some of the pick guard screw holes still don’t line up, so I just gave up and drilled them where they belonged because that actually does work provided the screw isn’t supporting any real weight or stress.
The problem with drilling into PLA is that after a certain speed the friction of the drill bit in the plastic just causes the plastic to melt and not behave the way wood or even metal would because the melted plastic isn’t ejected from the channels in the bit properly. It works if you take it slow and you may need to manually pull plastic bits out of the hole. The right solution is to fix the hole positions, but that was an exercise in frustration due to my limited skills as a 3D designer.
Gluing the Parts
The glue I used was regular old Krazy Glue that I got from the hardware store, and I can tell you that I used two full tubes of it for the guitar body. Additionally, gluing the black part to the yellow/red assembly was a tricky operation because the glue makes the parts slippery at first and it’s very easy to let the glue set with them misaligned. If I were to do this again I would alter the individual pieces so that they interlocked somehow. I have some ideas on that if there’s a next time.
Using simple finger strength worked for me, but then I have pretty long fingers and years of guitar playing has given me a strong grip in my left hand, so it it worked out fine. Your mileage may vary.
Total time stressing over and planning for the glue steps? About a day. Total time spent gluing? About 15 minutes. Measure 20 times; cut once, and all that. And yes, I had super glue all over my fingers when I was done but managed not to glue myself together and I didn’t imprint my fingerprints anywhere on the guitar.
Cost of the Project
Cost of Filament
Ignoring the cost of the printer (which was significant according to my wife), the cost of the filament is calculated to the penny by Cura, the slicing software I used to send the 3D models to the printer. Here’s how that worked out:
- MatterHackers Pro PLA 1kg roll (MatterHackers): $42.00
- Ultimaker Tough PLA .75kg roll (MatterHackers): $49.95
Note that these prices do not included the two failed parts due to a power failure and a tangled spool of filament, nor do they include the three purple parts I printed when trying to figure out why the loaded pick guard wouldn’t fit on the body. In other words, this price reflects a working model with no mistakes having ever been made. You know, just like my marriage.
Cost of Hardware
The total cost for the hardware that I used is shown here:
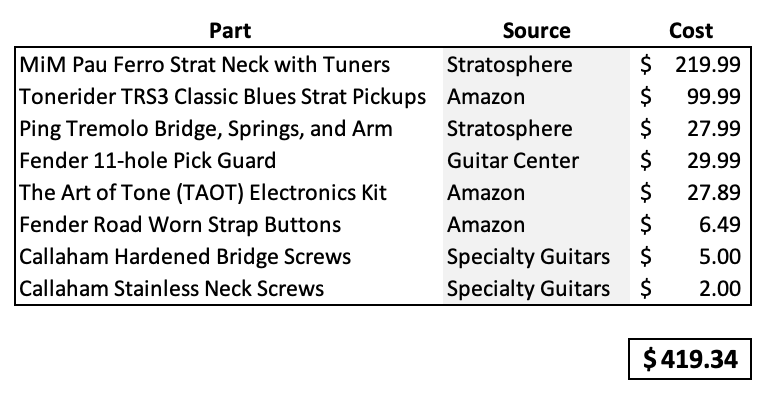
- MIM Pau Ferro Strat Neck with Tuners (Stratosphere)
- Tonerider TRS3 Classic Blues Strat Pickups (Amazon)
- Ping Tremolo Bridge, Springs and Arm (Stratosphere)
- Fender 11-hole Pick Guard (Guitar Center)
- The Art of Tone Electronics kit (Amazon)
- Fender Road Worn Strap Buttons (Amazon)
- Callaham Hardened Bridge Screws (Specialty Guitars)
- Callaham stainless Neck Screws (Specialty Guitars)
Total Cost for the Guitar
Let’s recap and get a grand total:
- Total cost of hardware: $419.34
- Total cost of filament: $73.61
Total cost for the guitar: $492.95
Sweet Cats! I could have bought a nice used Japanese or Mexican Strat for that price!
Remember, though, that over ¾ of the hardware cost is contained in just the neck and pickups, and both could have been much cheaper had I gone with 100% generic or low-cost solutions. There are plenty of $100 generic or even Fender Squire necks on Reverb and I could have easily sourced a set of no-name import pickups for $20. Hell, I could have made the guitar a single or even dual humbucker setup and done the electronics for essentially nothing since I have so many of those laying around. Had I been able to build this entirely with leftover parts, I could have called it “free” except for the $88.76 filament cost.
Things I learned While Printing
Nozzle Size Matters
If you’re printing big things like this and you’re OK loosing a bit of detail, get yourself an 0.8mm nozzle. Holy crap did that save a lot of time! For example, the lower purple horn takes 11h 25m to print with a 0.4mm nozzle and 5h 33m to print with an 0.8mm nozzle. When printing five huge parts that take 11+ hours to print, the total print time difference is measured in days.
The downside to printing with the 0.8mm nozzle at 0.4mm (you generally only print at a layer height 1/2 the size of the nozzle) is that trying to print small round holes such as those for the pick guard is difficult at best. Another problem with the larger layer height is that it’s harder to glue the pieces together because they tend to slide into each other’s grooves and since the grooves are larger, there’s more sanding that needs to be done. The biggest issue, though, is that the parts just don’t look as good. That’s why the red, blue, and yellow parts were all printed with a 0.2mm layer height while the black and purple (which are mostly behind the pick guard) were printed at 0.4mm.
Power Failures Suck
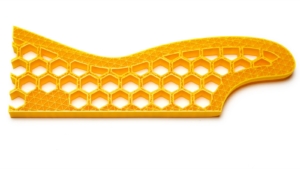
When I went to print first the full-sized piece (a 19 hour affair, remember) we had a power failure seven hours in which led to the first of two failed pieces, which you can see here in this pic. The cool thing about failed pieces is that they’re good for showing people the infill patterns that comprise the areas would be solid if created with subtractive manufacturing such as cutting, sanding, or CNC milling wood.
Drilling into PLA Doesn’t work Well
After trying in vain to get all of the pick guard holes to line up with my model, I finally gave up on about five of them and decided to just drill them out. This has two problems: first, if you don’t design a hole in the right place you may well drill into empty air due to the “solid” parts of the model actually being an infill pattern, and second, a spinning drill bit actually melts PLA plastic instead of drilling into it due to the relatively low melting point of PLA. Drilling slowly helps, and thankfully the holes I drilled were for the pick guard so they don’t really need to support any stress.
Source Material Matters
Tangled Spools Suck
pain lesson to be learned.
Keyed Parts Would be Better
Just gluing the parts together leaves a lot of room for error in the final stage, so if I ever print another I’ll be altering the parts so that they interlock in some fashion. I didn’t do this at first due to a lack of experience both in design and assembly of large 3D printed projects.
Be Careful Sanding the Parts
On the second guitar I built, I over-sanded one of the pieces so it doesn’t fit together quite right, the result of which can be seen in this picture of that second guitar where the blue and red parts don’t quite connect. That sucks because that blue part took 19 hours to print and I almost ruined it in a matter of minutes. If this had been a job for a client the entire thing would have been ruined because I didn’t notice the problem until gluing the third piece.
Sometimes Cheap is OK
The difference in price alone between those two part sub sets is $157.87 (Pickups: $99.99, Electronics: $27.89, Guard: $29.99) vs $39.99 (link) which comes out to $117.88 less, not to mention the time saved not having to wire up the guard. Not only that, but the smaller import pots fit into one of the old test pieces that didn’t work in the first guitar, so if I’d used a cheap import solution I could have saved days of design and reprinting.
The first picture is of the Fender guard with the $100 Tonerider pickups and TAOT electronics all hand-soldered by me.
I did have an issue when I printed all of the pickup covers. I discovered that on the import pre-wired guard that the bridge pickup had 52mm pole-piece spacing while the neck and middle were both 50mm, so I had to re-print those (the ToneRiders in my hand-wired setup were all 52mm).
The one place where I would not skimp is the neck, though I’d have to imagine that a nice Warmoth neck would do the job just fine.
But is it Useful as a Guitar?
The final guitar is well balanced, plays pretty much like a Strat, has a surprising amount of sustain, and actually sounds pretty great! It even suffers from Stratitis due to the vintage-spec pole piece heights on the pickups I used and when I listen to recordings I think the pickups need to be lowered, but I’m honestly kind of blown away by how well it works, which is honestly probably more to do with the genius of Leo Fender than anything I did.
The pictured sunburst guitar (technically Sienna Burst) is my 2008 Fender American Deluxe Ash Strat. I’ve modified the electronics and plastic which make the guitar a fabulous instrument and remains the only Strat that I’ve ever purchased. It sounds, looks, and plays amazingly well, so I used this guitar as the basis for comparison against the 3D-printed guitars.
You may notice that in my pics the tremolo arm is not attached, and that’s even true on my Fender Strat. Why? Because I’m a child of the ’80s when the Floyd Rose ruled the earth and I can’t stand the trem on a Strat. As a result, I tend to either deck the trem or just not use the bar.
I can tell you that the tremolo absolutely does work on the 3D printed guitar, but after testing it I immediately took the bar off and bolted the trem flat to the top. This is partly due to my dislike for the regular Strat trem and partly due to me thinking that six screws threaded into plastic probably don’t need the additional stress of me banging on the whammy bar.
No matter how impressive the material, I don’t think any plastic will compare with a nice piece of swamp ash, so my expectations were pretty low when I started playing the plastic guitar for the first time.
Quick Aside #2
Sure, I could have just put the guitar next to an amp that everyone recognized or took a picture of me holding it but all my amps are in storage except for my Axe-FX, and thanks to the salons all being closed due to the state-wide lockdowns I’m no longer pretty enough to be photographed.
Playability
This guitar does not have a refined feel like a nice wooden Strat, though it doesn’t have the candy-coated shell feeling of thick poly like the Fender does, either. And it certainly doesn’t have the luxurious feel of a lacquer-coated vintage instrument. My main gripe is probably the missing forearm bevel, but aside from that I feel like I’m playing a damn Strat.
The finished guitar weighs in at 6 lbs 10 oz (3.0 kilos) so it’s pretty lightweight for a Strat, at least when compared to the ash models that I prefer. Hell, my Judah EVH Frankenstrat weighs 8lbs 5oz (3.77 kilos) so it’s almost 25% lighter than that. The guitar is also surprisingly well balanced while sitting and standing, and I gotta say that surprised me, too.
2021 Edit: I’ve since resolved this problem which is commonly referred to as “Elephant Foot” in 3D printing circles. If your 3D printer is well setup, you shouldn’t have this problem.
The guitar is fairly resonant, but certainly doesn’t ring out like my ash Strat does, and the g-string seems a bit dead which I at first attributed to the high vintage pole pieces, but that didn’t seem to go away when I lowered the pickups down to the guard.
The guitar intonates well and the notes mostly play clear with the exception of some slight buzzing on the low frets which I attribute to neck relief. Honestly I haven’t really fine-tuned the setup because the guitar plays pretty well out of the box. I imagine it could probably be tightened up a bit here and there, but in reality this guitar will probably hang on the wall until someone asks to see or play it, so I’m not overly concerned about the details.
As a final note, it seems that every day I pick it up I need to tune it, but it doesn’t go out of tune while I’m playing it so that doesn’t seem like a major issue to me unless it’s a sign of the guitar slowly warping under the stress of the strings. Time will tell.
But How’s it Sound?
Even unplugged the guitar sounds like a Strat. Hell, even when I was walking around with nothing but the little black center piece bolted to the neck it sounded like a Strat! I honestly expected the finished guitar to sound like cheap plinky garbage but it does not. Plugged in it sounds like a Strat.
Now, I’m perfectly willing to blame my claim on a lack of a critical ear when it comes to Strats, being a humbucker guy at heart, but I generally pick up my Strat when I’m playing Dire Straits or even John Mayer, and to me this guitar does the job pretty damn well. Surprisingly well, in fact. Don’t believe me? Listen for yourself.
’59 Bassman
Open Chords #1
Open Chords #2
7th Chords
A Barre Chords
D-Shape Chords
Gary Killed a Little Lamb
For most of the recordings I play my usual test chords through all five of the pickup settings in the following order:
- Neck (position 5)
- Neck & Middle (position 4)
- Middle (position 3)
- Middle & Bridge (position 2)
- Bridge (position 1)
Why did I do them in reverse order of the numbered positions? Because I always record my guitars in the same order: neck to bridge.
For the last recording, I murdered Stevie Ray Vaughn’s Mary had a Little Lamb and put my own terrible spin on it in order to show off the fact that aside from building the guitar(s) in this article, I haven’t picked up a guitar in months. In fact, listening to those awful recordings I only hear a terrible guitar player and not a plastic home-made guitar. That’s gotta count for something, right?
Conclusion
I 3D printed a guitar! And it works! How cool is that?
Purists may argue that since I didn’t print the neck that I didn’t print the entire guitar, and to them I would say that a purely 3D printed guitar would probably look and sound like crap and I just couldn’t see the point of spending all this time and energy on something I wouldn’t actually play. Clearly I couldn’t see the point of practicing during the Coronavirus lockdown time, either, if the previous recordings are any indication.
Would I recommend a project of this size to the average person who’s new to 3D printing? Maybe not, but if you’ve had your printer for a while and you’re prepared for failed prints and other mishaps, then have at it! Especially if you already have most or all of the hardware you need to make it happen.
Would I gig with this guitar? Maybe for a song to show it off, but I’d have to do a lot of testing before I trusted it for an entire gig and I have my doubts that it would stand up to as much abuse and a wooden guitar.
Would I do it again? Hell, I already have! I printed a second almost identical guitar for my daughter because I had basically 3/4 of one already done due to test prints and such. That one even has locking tuners and doesn’t have Krazy Glue marks all over the back, even if I did over-sand one of the pieces.
My only concern is that PLA is known to warp under prolonged stress, so I’m not sure how long the bodies will last but so far it’s been a month with no discernible issues. If there are any failures in the future I’ll be sure to update this article. Of course the best part is that if it fails I can just print a new one!
April 5, 2021 Update: One Year Later
The last time I picked it up was probably six months ago when I moved it for reasons that escape me as I write this, but the guitar has only been picked up, tunes, and strummed a couple of times to show it to people. Sadly, since we’re over a year into Covid lockdowns, those were via zoom. The picture shows proof of one year’s worth of dust under the strings. Ew.
Here’s how the guitar has fared structurally:
- Glue seams – No change
- Plastic (PLA) warping – No change
- Plastic (PLA) cracking – No change
- Bridge angle and stability – No change
- Neck angle – No change
Here’s how the guitar fared from a setup standpoint:
- Neck relief – Slightly bowed: needed 1/2 turn truss rod adjustment
- Fretboard – A bit dry and could use some bore oil
- Frets – Could use a polishing
- Electronics – No problems
I find it pretty funny that though I fully expected the string tension to pull the PLA apart, there has been zero sign of that happening. Meanwhile the old-school wooden neck was the source of all of the issues with the guitar, but to be fair any guitar left in the corner for a year would probably need a similar setup.
I must say that I’m impressed. This glued-together 3D printed guitar still kicks ass a year after I made it, and you know what? It still sounds like a Strat!
June 2, 2025 Update: Five Years!
- Glue seams – No change
- Plastic (PLA) warping – No change
- Plastic (PLA) cracking – No change
- Bridge angle and stability – No change
- Neck angle – No change
Here’s how the guitar fared from a setup standpoint:
- Neck relief – Still straight! And this guitar is not in the humidified room with the nice acoustics.
- Fretboard – A bit dry and could use some bore oil (I hate dry fretboards)
- Frets – Could still use a polishing
- Electronics – It’s buzzing (ground hum), and it’s pretty bad. My guess without taking the guard off is that there’s a broken ground lead somewhere and while I’d be inclined to blame the cheap import parts, it could also just as easily be a bad solder joint from the maniac who built it.
The craziest thing of all? It was almost in tune. If the Tough-PLA had warped I would expect the guitar to be violently out of tune but it required only less than a semitone on a few strings, and what’s more it was perfectly playable. To be fair I don’t recall the last time I tuned it, but it’s been at least a year. Hooray for locking tuners, I suppose.
I’m honestly shocked. I expected this thing to self destruct within six months but it still plays well and aside from the probably grounding issue, it still sounds like a Strat. If I remember I’ll post another update at the 10-year mark, but short of leaving this in a hot car where it might melt, I’d imagine that the guitar has pretty well stabilized.
Donate: PayPal Crypto:
ETH: 0x0AC57f8e0A49dc06Ed4f7926d169342ec4FCd461
Doge: DFWpLqMr6QF67t4wRzvTtNd8UDwjGTQBGs
Very cool and I love the colors. Thanks for including enough geeky stuff to satisfy my nerdy side while still keeping it interesting. Look forward to seeing the next one.
A fantastic project and very nice documentation. Superb work, Gary!
Out of tune issue could be due to a higher coefficient of thermal expansion for plastics as compared to hardwoods. Even my ash-bodied Telecaster changes tuning (ever so slightly) after I’ve played it for 20-30 minutes as my body warms it up. It’s subtle, but measurable.
Like Dave C., I love the colors too! Great choices.
Continued …
To test this, tune the instrument and keep it temperature stable as long as feasible. Recheck tuning. If no change, good. If there is a change, it may be that the body is slowly deforming under pressure. This may reach a limit over time, though, and eventually stabilize.
Keep it in tune and keep us posted!
Interesting. If you mean “leave it in the corner and see how it does”, then I’m all over it. 🙂
Hi Gary,
I saw your Guitar on FB and was curious on how you 3-D printed it. You have a very informative style of writing. Excellent article. Nice job.
Take care ~ Dennis
Ps. ~ also liked your face masks. Can you modify them so there is a pouch to put “breathable medicine” in. If this virus comes out on droplets then why can’t we reverse that and send our cures in through our air ways directly into our lungs?
Just a thought.
Wonderful Guitar. Please make a video on youtube.
You ROCK!!! Agreed that a YouTube video would be awesome 🤘🤘
fat
Hi Gary.
It would be great to be able to mod this design. Any chance of posting in the TinkerCAD gallery?
https://blog.tinkercad.com/share-your-designs-with-the-world
I really enjoyed reading this and it makes me want to learn how to play guitar.
Ok, I am new to the guitar world, but not to 3d printing. My friend’s birthday is coming up in a couple of months and I was just hoping I could throw some dumb questions out there.
I understand the printing process and I will manage through that but for the assembly of the rest of the guitar do you have any good tips or videos on how to assemble the electric part of the guitar. Is this electric or what? Sorry this may seem like really dumb questions to you guys but I don’t know much of anything about guitars. Thanks so much in advance
You could maybe used heat sets fro attaching the pick guard on future design mods. They can be bought in various sizes and are pressed into the PLA with a hot soldering iron. They are a good strong solution.
Cool idea – thanks!
Very impressive, Nice job !!!
First part done. I’m printing this with a 0.2mm nozzle so I’m looking at around 360 hours in total. The quality is pretty amazing on my Ender 5 though.
I’m nowhere near proficient enough on any kind of guitar to justify spending out on genuine electronics so I’ll be going with generics. If you have any tips on where to get a neck and what to look for I’d be grateful.
360 hours! I’d love to see it when you’re done!
I got my neck at Stratosphere (see the Cost of Hardware section) where they have a whole bunch of options. Warmoth is always a good option, too.
I built two of these, one with nicer pickups and one with a generic populated pickguard from Amazon (see “Sometimes Cheap is OK” near the bottom) for for $40 and it’s surprisingly pretty great.
Hello, nice guitar, could you please send me the original (not sliced model). I’d like to split this model differently and make tonguing and grooving connections.
Sure! But only if you promise to share. 🙂
Very nice looking! I just printed one myself using – https://www.thingiverse.com/thing:4577188 – dues to me having an Ender 5 and the bed is just so small for things like this! I found this article when researching the best glue for putting it together (I am going to try JB Weld ClearWeld *crosses fingers*). I really hope mine looks even 1/10 as nice as yours! I do plan on painting it before adding everything just so it will fill in some small layer lines and imperfections (used .28mm layer height). Will have a make up on thingiverse when i get it done (if it doesn’t shatter into a thousand pieces anyway). Really appreciate the in-depth article for your process!
Keying parts is simple. Make matching 2mm x5 holes in both parts, cut any filament to 10mm lenght, insert and there it is.
I’m printing my own design guitar right now. First has cheap chinese wood neck, embedded Mooer PE100 multi effect (I hate cables and I can’t rip Marshall100 in multi apartment building aniway 🙂 . Its’s ok, sounds nice, plays easy, but it is not what I wanted. Second one, now in the making, will have printed PACF neck, PLA fretboard (with metal frets) and active humbuckers. I like to push myself…..
Thanks! I’ve since learned this trick (and it’s a great one!), but just wanted to add that since I use 3mm filament that the holes need to be ~3.5mm or 3mm and drilled out to better match the actual size.
I’d love to see your finished product! A printed neck is a tough one to pull of and would love to see it.
Hi
For now it is here:
https://www.pinterest.co.uk/stenc55/my-3d-printed-guitars/
I’ll have to redo the neck. Right side tuners are to close together, neck mounting holes will have to be strengthened, and most important, instead of 2x fi6mm rods I will put in 2x 10x5mm rods. It likes to bend too much.
Whoa – that’s cool!
I find bore oil a bit too oily. Dunlop lemon oil is my go to.
Hello,
you did an amazing job designing this guitar and thank you for sharing this inspiring project.
I would love to be able to design my own guitar but I never assembled one (I have basic knowledge of Fusion 360).
I would like to know how you got the dimensions to ensure that the neck, microphones and other parts fit well?
Do you have a file that I could use and modify with my own design?
Yours is pretty cool and I would be happy to use it but I would be much more proud of myself if I could create my own design.
Thanks a lot.
Xavier
Thanks!
Sorry, I don’t have what you’re looking for, but the body is a Fender Stratocaster shape, so there should be a lot of information out there about them. A quick search found this which would probably be a good starting point: https://theelectricluthier.com/your-guide-to-build-and-shape-a-stratocaster-body/
Have you had any issues with PLA melting? I printed one for my significant other and he is concerned about it melting!
Nope! The melting temp of PLA is ~170C which is 338F, so for it to spontaneously melt it would need to be in an oven. Even the dashboard of a car in Arizona in the hottest summer days only gets to ~195F.
If it does melt, though, just print a new one! 🙂
Hi,
Whats the size for the guitar. I see 459 for x 320 for y and 44 for z.
Its very small for a strat no ?
Hey Gary,
What an awesome way to use 3d printing! I came across your Thingiverse file the other day and was just blown away by how nice and easy the printing appeared. After doing some more research and seeing your well done writeup I’m convinced to take the plunge into this project. I’ve been reworking your model to hollow the top honeycombing out to allow for a resin pour and even possibly do the main body in resin as well if possible. Assembling them with some joints and keeping the components sections and rim 3dprinted.
Thanks again!
Very cool! I’d love to see the finished product.
Man I just stumble upon this article and blew my mind! Very cool I wanna make one myself!
Did you ever make the YouTube video?
I did not, but that guitar is still going strong!
What was the scale length of the neck you used?
Details from the link where I outlined the parts: Official Fender Player Stratocaster Neck & Tuners- Tinted Maple w/ Pau Ferro Fingerboard- Modern “C” Shape- 9.5″ Radius (241 mm)- 22 Medium Jumbo Frets- 25.5″ (648 mm) Scale Length– 1.650″ (42 mm) Width at Nut. Satin Urethane Finish on Back, Gloss Urethane Finish on Front.
Hope that helps!
Hİ, it looks great, I’m about to place the order for the neck and other parts. I have only one question: what is the tremolo measurement? (52.5mm 54mm)
I see that Stratosphereparts.com is no more so my links don’t work. Such is the way of the web. They seem to still be selling on Ebay, though.
I don’t have that measurement in my notes, but the bridge I used is a Ping STR-TRST11-C which is for American Vintage Stratocasters.
Thank you for your response, I need the distance between the first screw and the last screw, it’s not written their either :S The holes didn’t line up for me, I have 52.5, I think I need 54.
That’s the bridge I used. I can’t measure accurately without de-stringing but it looks more like 55-56mm which makes sense since according to Fender the American Vintage bridge is 2-7/32″ or 2.22″ which is 56.388mm.
Fender link: https://www.fender.com/en-US/parts/bridges/american-vintage-series-stratocaster-tremolo-assemblies/0992049000.html
I can’t access the site you shared, that’s why I can’t see it :S
It doesn’t surprise me that the guitar sounds like a Strat! 🙂
Recommend checking out this video if you haven’t already seen it. The main conclusion is that the only thing that really matters on a guitar is the pickups and electronics (as well as strings, and scale length).
https://youtu.be/n02tImce3AE?si=v37Z0h132yfbKvdD
Just wondering how you attached the Strap Buttons to the guitar. Very cool….making one as we speak 🙂
I drilled a hole and screwed it in.
Hey, I was wondering how that “Strong PLA” is holding up without metal supports like the EXO Guitar? I’ve been thinking about making my own but I’m concerned about it becoming deformed after a while.
Thanks for asking! I’ve posted a five-year update at the end of the article.